The top business objective of any organisation is to maximise profits through effective and optimal use of resources such as physical assets and inputs. Nonetheless, some organisations lack the resources to audit their existing equipment and manpower before making significant investments on physical assets to meet their growing demands. This could result in high capital expenditure (CapEx) but low return on investment (ROI) due to excess capacity and underutilisation of equipment at the production floor. In other words, you may have made a costly mistake.
Thankfully, there is a better way to decide when, what and which investments to make. Overall Equipment Effectiveness (OEE) is used by manufacturers around the world to answer questions such as:
- How efficient is your production line and equipment
- How are machine downtime affecting your productivity
- What are the other factors affecting your productivity
- How can you better allocate resources​
In our experience, here are three practical ways in which OEE can maximise the earning power of your facility and generate positive financial impacts for you.
1. Achieving the right ROI on your equipment
With growing demand from clients, organisations may be tempted to use their savings to finance new equipment and capture business opportunities. Such a move may seem even more pertinent when existing pieces of machinery do not seem to be able to produce as fast as they should…
While new pieces of machinery may increase production speed, we are, however, aware that CapEx on physical asset is expensive and there are risks incurred. Before diving headlong into new investments, it would be prudent to use OEE to find out how much unused resources are available in your factory and what is causing a delay in your production speed.
According to use cases, the average OEE of production lines and machines hover between 40 to 60%. Having a low OEE is not a serious concern if you are aware and actively implementing changes to improve it. The danger lies when you are unaware that your machines are not producing as fast and as effectively as they should — an OEE score of below 50% could imply that you are incurring unnecessary costs from production losses and (possibly) doubling your payback period.

As demonstrated, OEE can provide a fair comparison between your actual production and the theoretical maximum production. By taking into account contribution margins, you can forecast your net profit in an objective manner and derive ROI amidst other profitability metrics such as Return on Capital Employed (ROCE). If the manufacturing plant is not achieving an ideal ROI, it would be best to allocate resources to improve existing capital usage before making new make capital investments.
After investing in new equipment, OEE score could be used to monitor how efficient they are running, so as to extract the maximum ROI and reduce your payback period as much as possible.
2. Maximising profit by closing the gap between the production floor and management
The management wants to make decisions that would increase the profit of the organisation. The difficulty, however, lies in obtaining the insights to make such informed decisions.
Profitability depends on revenue and cost. As such, an output that fetches a higher price may not necessarily generate more profit because it is costly to manufacture. To accurately obtain profitability figures, the organisation would have to find a way to connect the production floor to the income statement in real-time. Using OEE score strategically can come in handy.
Imagine a situation where you are presented with the OEE score for three manufacturing equipment A, B, C, used on three different product lines. A has an OEE score of 40%, B is 50% and C is 60%. The most intuitive response would be to improve the equipment with the lowest OEE (aka A) followed by B then C.
To maximise profit, however, you should look into finding the improvement that would increase Income from Operations (IFO) by the most. For instance, improving equipment A’s OEE score from 40% to 55% may generate less profit than improving that of equipment C from 60% to 75%. You are able to find the relationship between OEE and profit if you feed the data collected into a
- Manufacturing Execution System (MES) or
- Enterprise Resource Planning (ERP) platform
Together with these resources, OEE and its host of real-time production floor data value-adds to the decision making process of both the production managers and the management. OEE also comes in helpful when you want to track how much equipment utilisation has improved while implementing change across your production floor.
3. Increasing profit by cutting cost
Having higher demand for your output would indisputably increase revenue (Units Sold x Sales Price), and in turn, increase profits. Demand, however, is an exogenous factor for profits since you cannot control how much clients would want your products. Costs, on the other hand, is an internal factor that you can control within your production floor. Decreasing costs would most definitely increase profits, ceteris paribus.
Cost savings can come from optimising workforce productivity. When operators are able to work more productively, fewer work shifts are needed and you can produce more with less.
A client from the food processing industry implemented our industry IoT systems on their production floor and was able to consolidate OEE scores in real-time, across all production lines. The OEE scores and its core components of Availability, Performance, and Quality are made known to all operators through a dashboard, such as the one shown here.
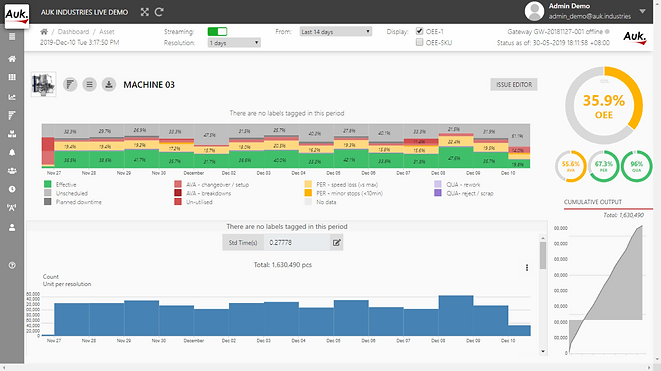
From there, they were able to gain insights on their peak and idling production time. With a small reshuffling of work schedule, they were able to increase their volume output by 34% (corresponding to an OEE increase from 55% to 75%). The quality of output has also improved through the data collected by the sensors attached to the food production machines. As such, there was less wastage due to rejects.
​Cost savings can also come from utilising your assets and resources more efficiently.
With OEE insights, you may discover that your production facility has the extra capacity (both physical and labour) to take on new projects or make more variants of products which are more profitable. This is called ‘uncovering your hidden factory’. Often times, a low OEE score is indicative of a big ‘hidden factory’.
‘Hidden factory’ refers to the idle capacity of your production facility; the extra amount of production that can be made without additional CapEx. It is often caused by
- Schedule Loss
- Availability Loss
- Performance Loss
- Quality Loss
By uncovering your hidden factory, you also stand to enjoy:
- Lower conversion costs: Your fixed cost is spread over more output
- Lower cost of inventory: With more effective run time, the lead time is reduced and inventory can be ordered on a more ‘just-in-time’ basis
- Deferred Spend: Increasing the throughput of existing equipment, increase ROI and defer spending on new machinery.
Traditionally, the production floor and management worked mostly in silos because there is a lack of resources to track the performance of their production floor and tie them in with financial performance. With real-time OEE, organisations can easily improve their production performance and improve business results, thereby achieving their profit goals more easily.
You can also join the OEE revolution and find out exactly how and where you can improve the financial performance of your manufacturing plant.