
SOFTWARE ANALYTICS
Deep-dive into data instantly with powerful software
Get straight into the system, get right into data and insights.
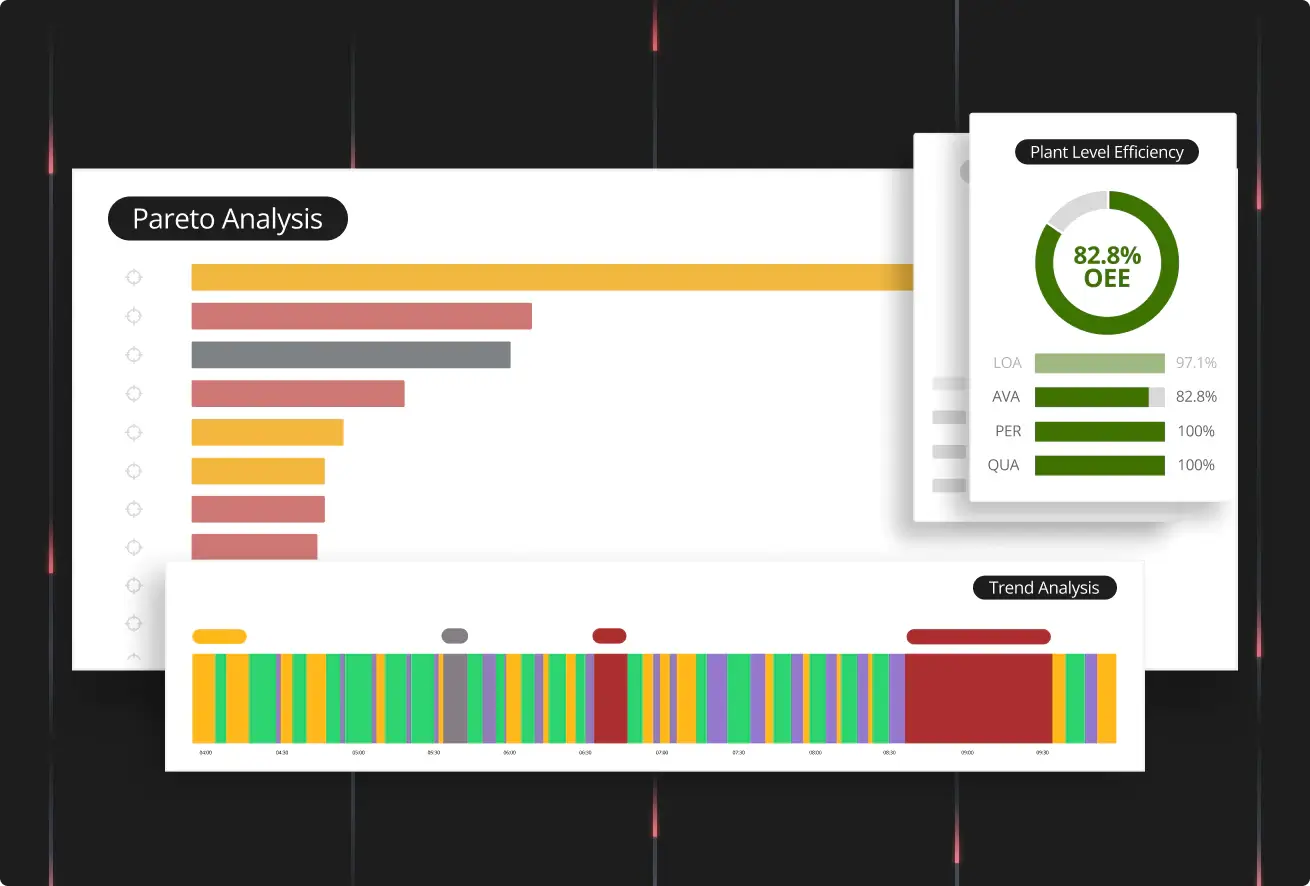
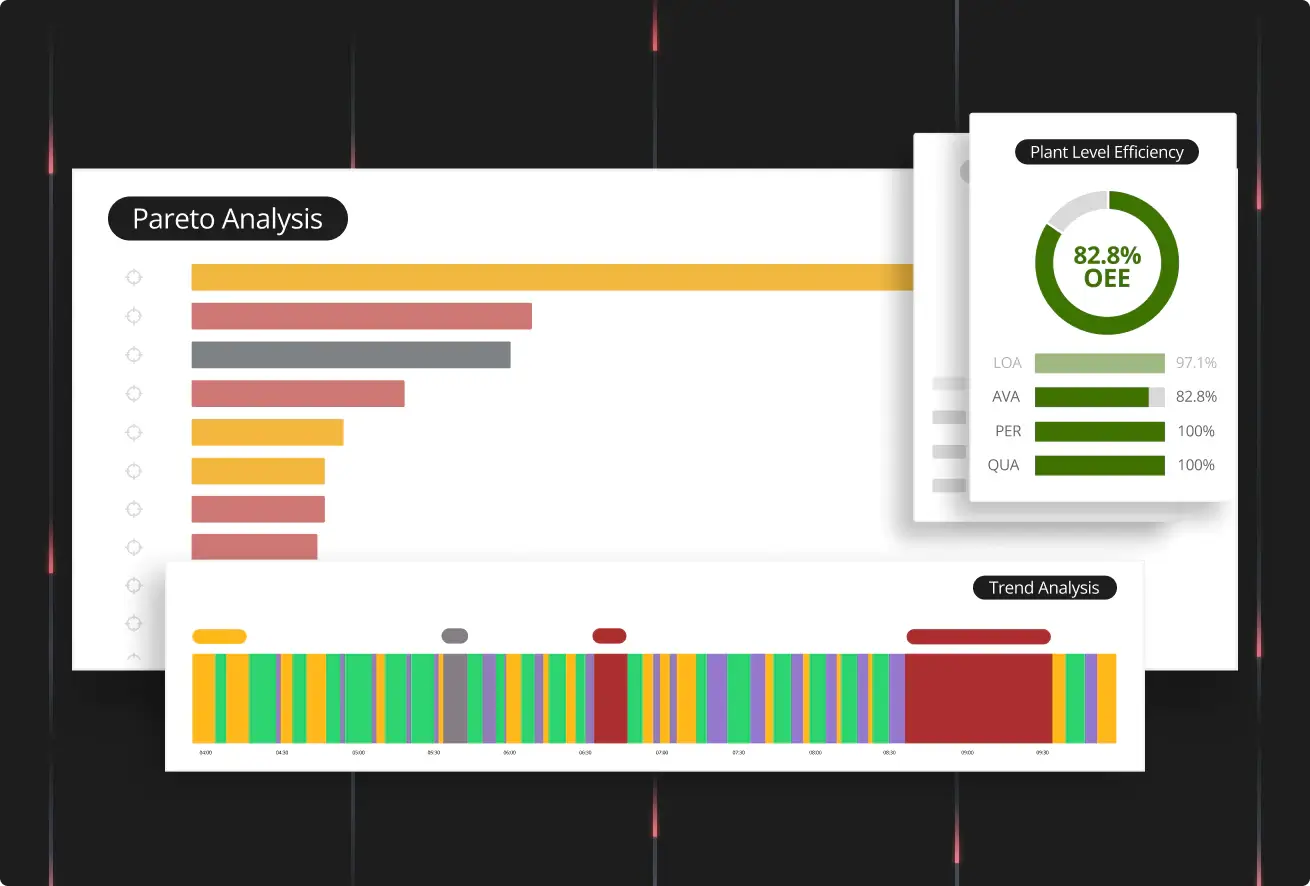
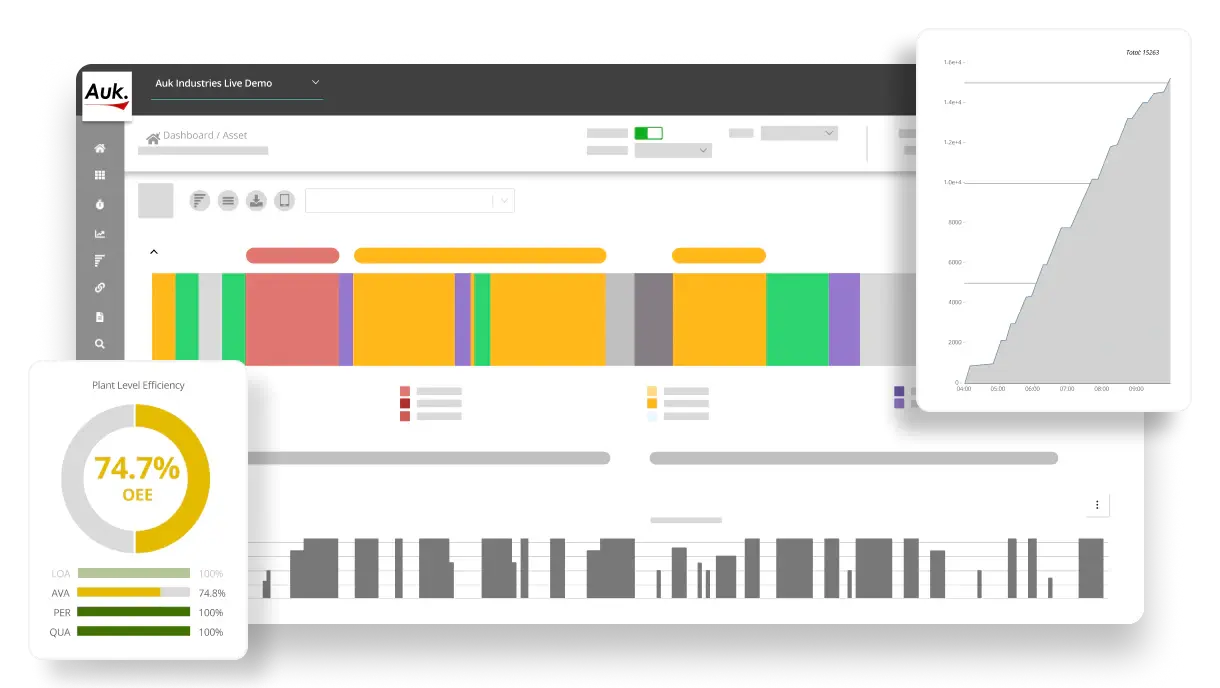
01
Single Asset Deep Dive
Our IoT edge processors capture 10,000 readings/second from connected sensors, tracing micro-stops and speed losses. Data is intelligently aggregated at the edge, providing all-time actual conditions.

Asset View
Observe single asset real-time data in resolutions as detailed as a few seconds or across the entire year.

Event Labelling
Users enhance machine data with event or issue definitions within an entity-wide hierarchy, enriching event information. Escalate easily to track issues for root-cause problem solving.

Product Tagging
Apply product-specific characteristics and factors by tagging product type or SKU onto the real-time data stream. Track work orders or lot IDs for improved traceability.
02
Baseline and Gap Analysis
Advanced algorithms analyze real-time streams with millions of data points, establishing product-specific standard cycle times and potential. Shop floor performance is continuously tracked.
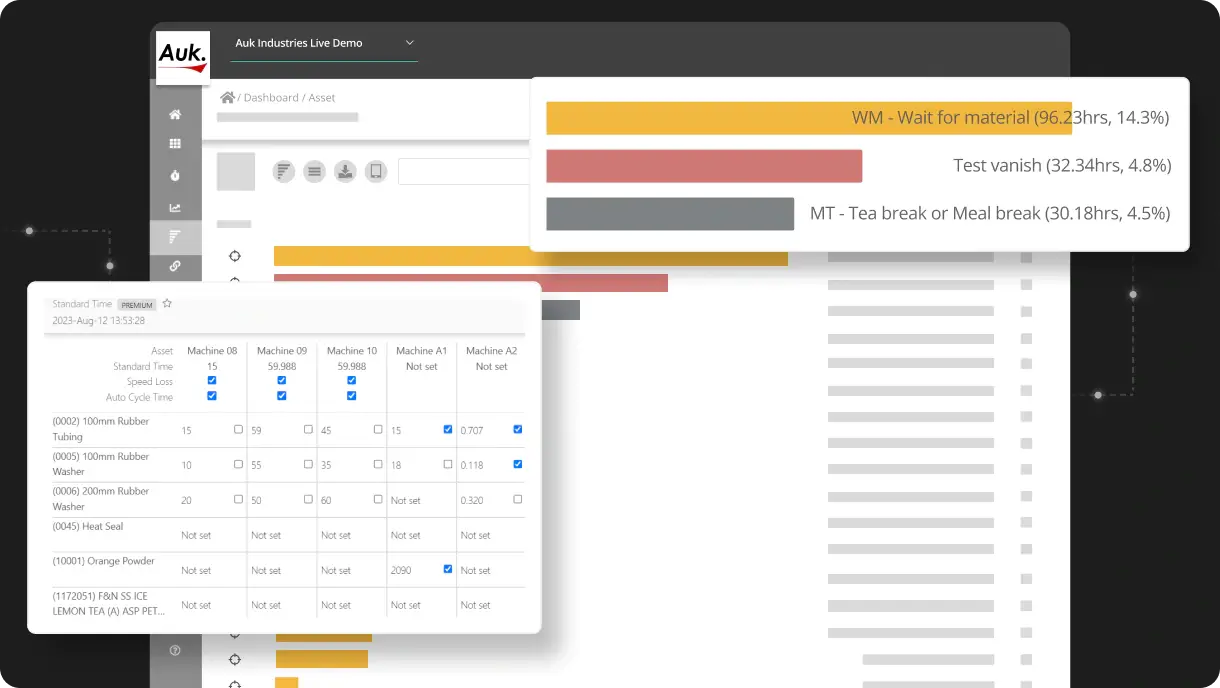

Standard Time Management
Differential product CT OEE analysis is critical in High Volume Low-Mid Mix manufacturing where various product ranges are produced using the same line.

Batch Cycle Recognition
Accurately define and capture batch cycle time, changeover time, and batches. Determine average idling or changeover time between batches.

Pareto Analysis
Deep dive into the top 20% reasons causing 80% of operational losses. Compare across shifts, production lines, and the entire factory.
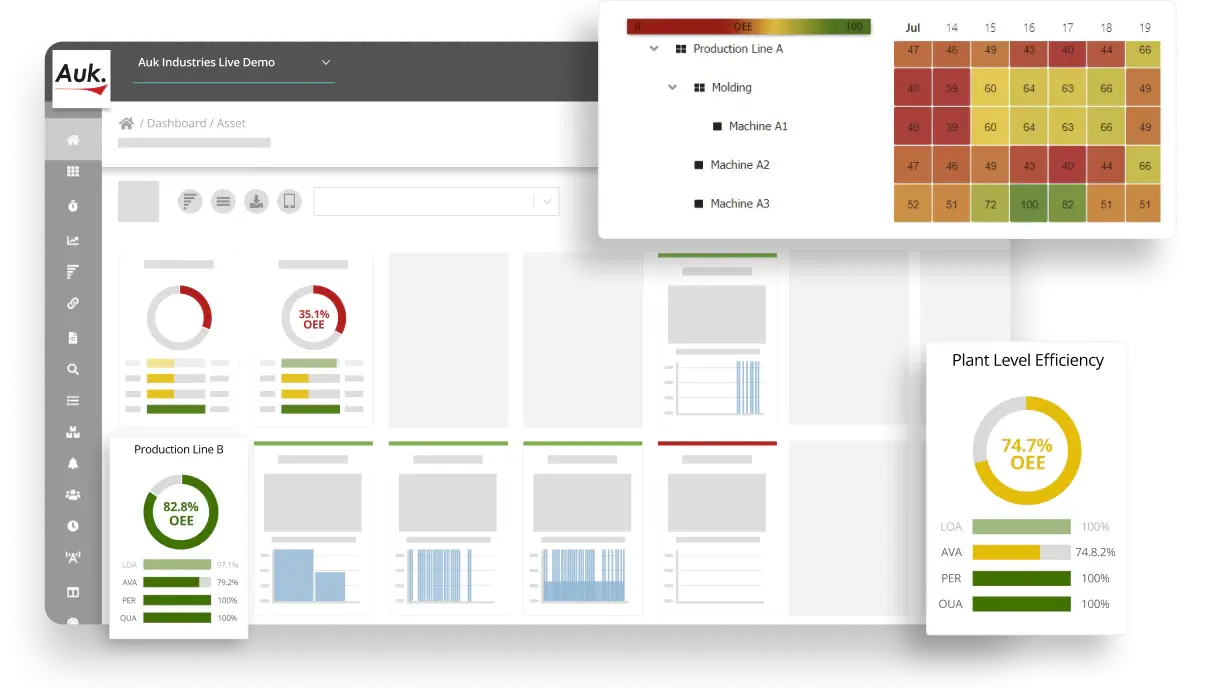
03
System-level Plant-wide Performance
We analyse assets from a macro and micro level to identify issues. So as to derive top plant-level performance and solve the most critical problems.

System-Level Block View
Study the individual utilization of each retort. Analyze the overall retort group performance.

Heat Map
Get a high-level glance at monthly plant performance in a single view. Easily identify critical lines or segments.

Multivariate Regression for ML
Perform detailed regression analysis of critical parameters and correlations among multiple process and machine health parameters, enabling corrective remedial actions to be taken.
Get more out of your factory operations today
Here’s why Auk will be the gamechanger for your operations
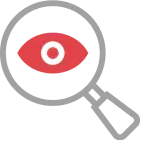
Complete operational transparency

Single source of truth across the enterprise

Real-time monitoring and alerts
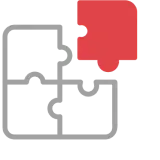
Prescriptive problem solving

Autonomous constraint/bottleneck identification

Deep data analysis on operational losses
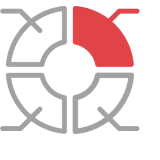
Closed-loop performance management

Digitized full P/D/C/A cycle

Cross-level KPI connection
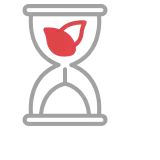
Future-proof ecosystemÂ

Lifetime software feature iteration

Full integration capability
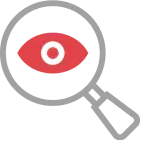
Complete operational transparency

Single source of truth across the enterprise

Real-time monitoring and alerts
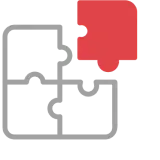
Prescriptive problem solving

Autonomous constraint/bottleneck identification

Deep data analysis on operational losses
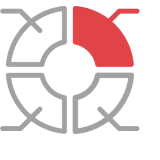
Closed-loop performance management

Digitized full P/D/C/A cycle

Cross-level KPI connection
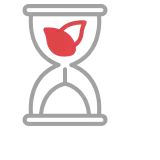
Future-proof ecosystemÂ

Lifetime software feature iteration

Full integration capability
API Integrations
Auk can be connected to leading industry software via API integration
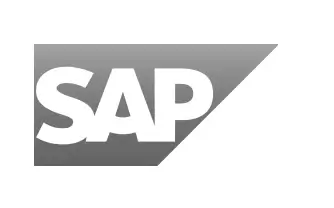
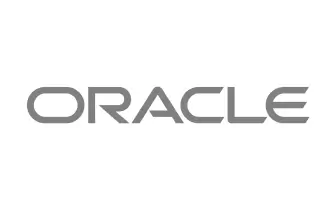
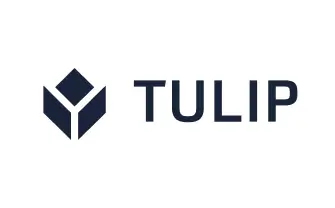
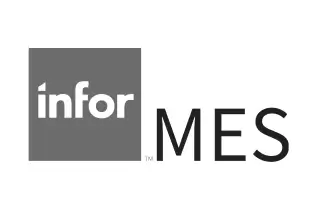
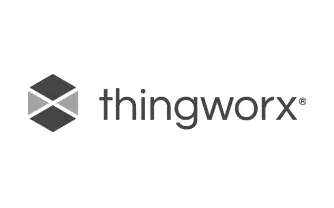
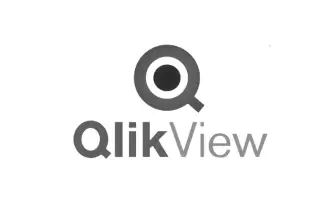
For all your operational goals, there’s Auk
With Auk, you get a hassle-free, powerful solution for your factory operation needs.







Top Frequently Asked Questions
We’ve partnered with manufacturing companies in diverse industries and successfully integrated machines, including older ones dating back to World War II.
Auk has experience in various industries, including:
- Food & Beverages
- Chemicals
- FMCG
- Automotive
- Metal Fabrication
- Injection Molding
- Medical Devices
- Semiconductors and Electronics
- Packaging
- Woodworking
- and more.
Auk’s technology is versatile and compatible with a wide range of machines, both old and modern, from various manufacturers.
Yes, our system operates effectively in varied environmental conditions. Our Edge IIoT devices are placed within machine control panels, ensuring protection alongside critical electronics like PLCs, relays, and VFDs. Our wireless mesh network for data transmission eliminates the need for extensive cabling infrastructure, ensuring device protection and system reliability.
Auk’s technology functions much like a ‘Fitbit for machines,’ focusing on three primary categories of data:
- Output: This mirrors the concept of counting a person’s steps but applies it to machines by tracking the quantity of cycles or products produced within a specific timeframe.
- Health: Similar to monitoring a person’s heart rate, this involves tracking a machine’s operating parameters, such as pressure, rpm, temperature, vibration, and current. These parameters are invaluable for quality control and machine health monitoring.
- Sleep Cycle: This category includes metrics like uptime, downtime, idle time, and changeover time. It provides insights into the machine’s operational patterns and efficiency.