In manufacturing, achieving consistent performance across shifts is a persistent challenge. While day shifts often benefit from robust supervision and support, night shifts can operate with less oversight, leaving untapped potential hidden in the shadows. This week, we’re thrilled to share a success story from one of our valued customers on how they turned transparency into transformative results.
The Challenge: Uneven Shift Performance
Our customer, a leading automotive parts manufacturer, faced a common industry hurdle: night shifts lacked the same level of visibility and supervision as day shifts, with office staff absent after hours. Production outputs appeared comparable between shifts on paper, but something didn’t add up.
With complete transparency, our customer uncovered a striking insight. During the first half of the night shift, production speed surged significantly higher than the day shift—only to taper off later, resulting in an overall output that matched the day shift’s steady pace. This pattern would have had gone unnoticed without granular, real-time data.
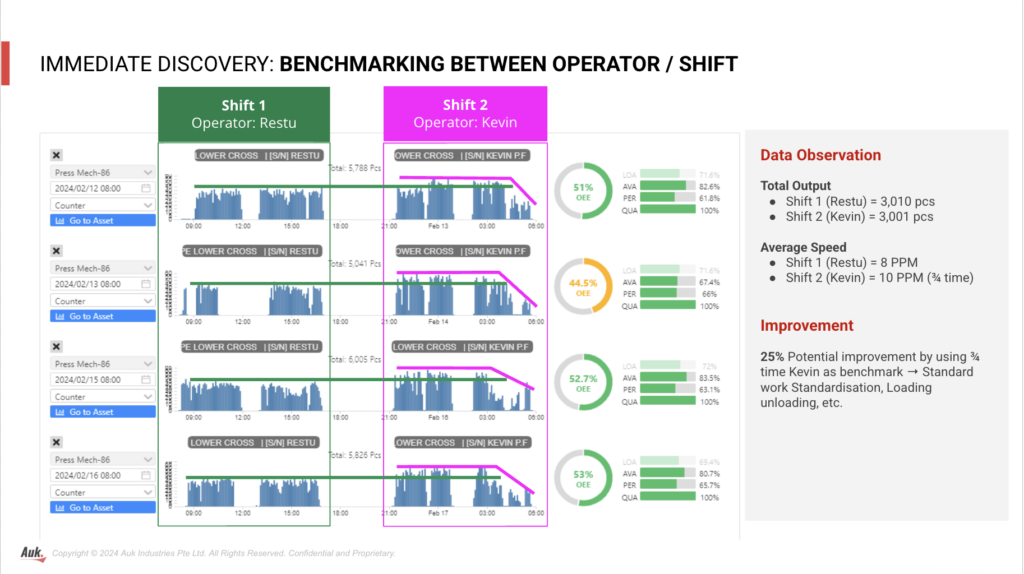
The Action: Benchmarking and Standardization
With this revelation, our customer took decisive action. They conducted in-depth benchmarking and cross-learning between day and night shift operators, identifying best practices that drove the night shift’s peak performance. By standardizing these techniques across both shifts, they eliminated inefficiencies and elevated output consistency.
The Result: A 25% OEE Boost
Within just two months, the impact was undeniable: a 25% improvement in OEE. Both shifts now operate at the higher production speed previously seen only fleetingly at night—unlocking capacity, boosting profitability, and setting a new standard for operational excellence.