The Internet of Things (IoT) has become the new catchphrase for all things Industry 4.0 related. Some are sceptical but it remains a fact that IoT has and will continue to generate enormous value for businesses, healthcare workers and even homemakers in the coming years.
Manufacturers around the globe are starting to understand the benefits of IoT-readiness – how IoT goes hand in hand with the digitalisation of manufacturing; from measuring output, energy consumption, wear and tear, to monitoring temperature, humidity and current usage trend within each machine. Together, newer and better ways of production and maintenance can be found to improve the efficiency of factories and the entire supply chain.
Despite its benefit, a significant percentage of manufacturers hesitate to embrace IoT. Their apprehension stems from the following areas:
- The concern that their existing machines cannot become IoT-ready
- Fear of incurring large expenses to have IoT-ready machine
Before jumping the gun to address and alleviate the above concerns which impede manufacturers from leaping towards IoT, it is crucial to first comprehend the meaning of IoT-ready machines.
What is an IoT-ready machine?
There are various explanations for an IoT-ready machine, but it can be best put as a machine with the ability to collect, track and ‘spit out’ real-time data when requested, anytime. The data collected is often used to generate timely insights.
”Xiaomi’s Roborock vacuum cleaner, fitness tracker, smart air-conditioner are all example of IoT-ready machines/devices. They collect and have real-time data which can be made readily available and accessible for their end users. The end users can then decide how to make best use of the data (e.g. control the temperature of the air-conditioner remotely).”
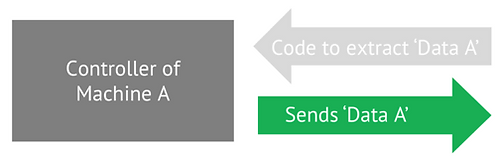
Some machines come pre-built with a controller (the ‘brain’) which gives it the capacity to ‘communicate’ with a computer and transfer the requested data.
Such is the case for many new machines (i.e. the latest models), but it is not without its troubles. Manufacturers regularly encounter problems extracting data from these controllers because:
- Strong technical expertise is necessary to ‘communicate’ with these controllers and access the data
- Hefty amounts of custom developer work are required to collect data from the controllers of different machines – the controllers differ for different types of machines and the companies that produced the machines.
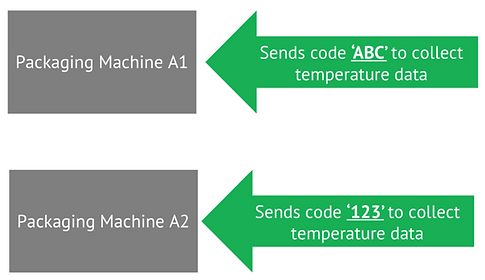
There are 2 packaging machines, A1 and B1. Though they are machines of the same type, A1 was produced by Company A whereas B1 was produced by Company B. The documentation and commands used to extract data from A1’s controller cannot be synonymously used to do the same for B1’s controller; B1’s controller requires its own set of instructions. As such, manufacturers with tens and hundreds of machines require an extensive amount of time and effort to ‘speak’ to the controllers and collect the necessary data. It is also common for machine vendors to ‘lock’ the access to their controllers, making data collection/extraction nearly impossible or extremely tedious.
Can my existing machines become IoT-ready?
Injection moulding machines, bottling machines and Computer Numerical Control (CNC) machines – many of these complex machines which are already residing on the production floor do not come with IoT readiness. Design and built before the emergence of Industry 4.0, these machines may not have the required internet connectivity and compatibility with visualisation for users to interact and make use of the real-time data available.
Despite this, all hope is not lost! These machines can become IoT-ready with the help of technology – the advent of universal IoT nodes have made it possible for everyday objects such as water heaters, ovens, as well as machines to be IoT ready within minutes and become ‘smarter’.
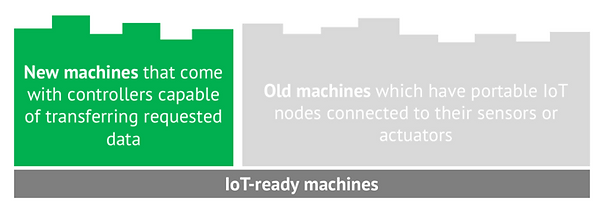
There are 2 groups of IoT-ready machines. The first group includes new machines with controllers which are capable of transferring requested data. The second group includes old machines which were not originally IoT-ready but have become so, after having universal IoT nodes attached to them.
By attaching these universal IoT nodes to the relevant I/O terminals (existing sensors/actuators) of the machines on the production floor, manufacturers can instantly collect important parameters such as temperature, pressure and output of machines and production lines. In turn, these invaluable data are transferred to the cloud and processed using advanced analytics to provide real-time insights for the manufacturing floor.
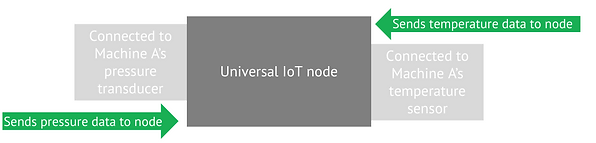
”The sensors and actuators of a machine are comparable to our ears and heart. Connecting universal IoT nodes to a machine’s sensors and actuators to collect data is akin to using an ear thermometer to measure the temperature of our body or a heart rate monitor to measure our heart rate.”
Inherently, machines of any type, brands or models (that are electrically powered) can become IoT-ready and start sending raw, unadulterated data to the cloud for processing and analysis, by simply deploying universal IoT devices that can read data from their existing sensors/actuators via the standard I/O terminals. This is especially important for production floors with a mix of newer machines which are IoT-ready and older machines which are not. Prior to the introduction of these universal IoT devices, manufacturers could only obtain limited data and insights from the newer machines and not the older ones.
“If only 10 out of 100 machines are new and IoT-ready, it would be difficult to analyse both the production lines and overall factory performance because manufacturers only have access to the data for 10% of the machines. This would result in lost opportunities for factory-wide/ global optimisation because data from the remaining 90% of machines are missing.”
Is it expensive to have IoT-ready machines?
The costs involved to have IoT-ready machines depend on the means of getting them. Some manufacturers would wholly replace their existing machines with new IoT-ready machines whereas others would choose to transform existing machines into IoT-ready machines by attaching universal IoT nodes to these machines’ sensors or actuators. The former would inevitably incur high CapEx while the latter method may be comparatively cheaper (depending on how you take data from machines, from controllers or from existing I/Os of sensors/actuators) because manufacturers would only have to pay for the IoT devices.
It is noteworthy that the growing adoption of IoT (usage has increased by more than sixfold from 2012 to 2014), alongside the entrance of new players in the field of industrial IoT solutions, has led to significant cost reductions in making machines IoT-ready. Companies, such as Auk Industries, for instance, have developed a plug-and-play Industrial IoT (IIoT) solution that can be self-deployed within minutes, significantly reducing the cost of adoption.
Manufacturers need to think beyond IoT-ready machines to maximise gains from IoT
According to market analysis, IoT is believed to create up to $3.7 trillion value per year for the manufacturing industry, from 2025 onwards. To successfully harvest the benefits of IoT, achieve optimised value chain activities and sustainable business results, manufacturers need more than just machines which are IoT-ready.
In the future, all machines (complex, non-complex, big or small) may come pre-built with IoT functionalities. This is good news, but a catch 22 situation remains – manufacturers need a standardised mean of collecting data from the various IoT-ready machines made by different producers, as well as a comprehensive processing and analytics platform which can synthesise various machine-level data and metrics into system-level metrics and insights.
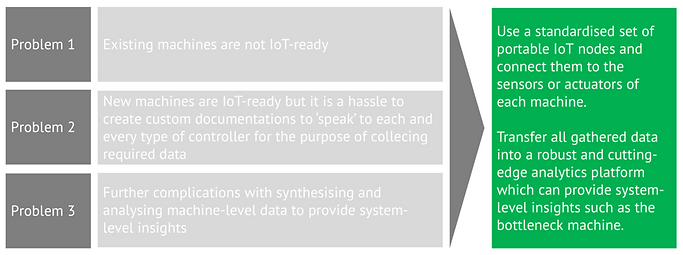
Nonetheless, the aforementioned universal IoT nodes could come in handy to resolve the sticky situation. By connecting universal IoT nodes directly to the sensors or actuators of any machines (be it pre-built IoT-ready machines or not), manufacturers can bypass the high complexity, high costs and long lead-time needed to gather data singly from each machine.
After which, the gathered real-time data should be transferred to a robust and cutting-edge analytics platform so that:
- Manufacturers have access to a single source of truth and can use it to make ‘smarter’ and more data-driven decisions – bid goodbye to making decisions based on instincts and subjectivity. It is recommended that manufacturers select an analytics platform with features such as in-built heat maps or Pareto charts which can identify the machines that are the main perpetrators of minor stops, speed losses, reworks, etc. These insights are usually unobtainable through the naked eyes and even the most experienced production floor managers may not be aware of them.
- Real-time intelligence such as the OEE of each production line can be displayed in a dashboard, allowing the production line managers to discover the poor-performing production lines right away, rather than to wait till the end of the day. Furthermore, the bottleneck machine in each production line can also be easily identified on the fly. This is a piece of valuable insight which operators can use and rectify the bottleneck issue.
- The performance and information of manufacturing plants across geographies may be remotely tracked, greatly improving transparency in the overall production chain, inventories and supply chain management.
- A repository of data on machine wear and tear can be stored as used for predictive maintenance, which is often more effective than time-based maintenance which disregards the real-time condition of each machine and its parts.
- Production status and downtimes may be shared with the original equipment manufacturer (OEM) customers so that they have sufficient response time to react to possible production delays while manufacturers can swiftly rectify any problems. This could help to build better relationships and rapport with downstream customers.
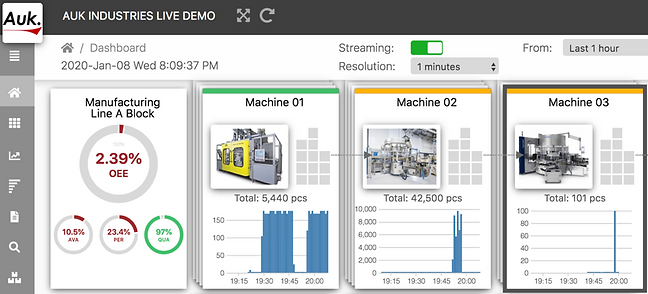
There are no hard and fast rules for manufacturers to adhere to when it comes to staying on top of the IoT curve but IoT-readiness should be the goal that manufacturers of all scales and sectors are working towards. Whether manufacturers are looking to achieve real-time intelligence, measure OEE or increase the transparency of their manufacturing plants, IoT-readiness is one of the most proven solutions at hand.
The ease of deploying universal IoT nodes have lowered the barrier for old machines to become IoT-ready and eased the difficulty of accessing data from new machines which are already IoT-ready. To achieve the remaining benefits of IoT and unlock the secret of being future-ready, manufacturers ought to integrate all incoming data with a reliable and future-proof analytics platform and implement strategies and improvements based on the insights gathered.