What is Industry 4.0?
“An ongoing digital transformation process where companies and organisations leverage disruptive digital technologies (e.g. Internet of Things (IoT), wireless sensor networks, big data, cloud computing, embedded system, augmented reality) to revolutionise the way their business operates and grows.
What does Industry 4.0 mean for manufacturers?
“Industry 4.0 turns the dream of developing an intelligent, connected, and efficient value chain into a reality.”
Digitalisation within the manufacturing industry is not new. Yet Industry 4.0 is more than merely digitalising manufacturing facilities. Through edge-cutting information technologies, operations technologies, and advanced data analytics, the Industry 4.0 movement empowers companies with critical business-intelligence and unparalleled competitive advantages: higher operational and production efficiency, high mix, mid-high volume production capabilities, and end-to-end connectivity within the manufacturing environment.
To go one step further and capture the most value out of Industry 4.0, manufacturers need to integrate three key areas: business strategy, technology, and people. This is achievable by implementing Industry 4.0 technologies vertically (strategy-organisation-culture) and horizontally (technology-human).
With that in place, we can now put ourselves in the shoes of the people (i.e. stakeholders in our manufacturing plant) and drill down on the specific values and benefits that are unlocked for each stakeholder, and in turn, the entire manufacturing facility.
Benefits of I4.0 technologies: for Business Owners, Operations Directors & Factory Managers
Most manufacturers around the world have yet to collect data in real-time. The most widely used method is to manually collect data at the end of each shift and have them consolidated by the line or section managers. Team reviews based on these aggregated data are usually conducted only a few days later to get a rough estimate of the factory’s performance.
For many managers and directors, such a data collection and feedback model can be frustrating. Manually collected data is unreliable and dated—they provide little opportunities for managers to find out when output or performance has fallen below the benchmark. As such, swift corrective actions to rectify the problems cannot be taken. Moreover, if something were to go wrong during a certain timeframe, it would be almost impossible to find out ‘why’ since data is only collected at the end of each shift.
Reliable plant data for analysis and performance improvements
To gather reliable plant data for analysis and performance improvements, Operations Directors and Factory Managers are turning towards quansi-real-time-performance data. By integrating IIoT to the factory floor, Directors and Managers can monitor the performance of each machine, production line and the entire plant at the snap of a finger. This visibility further allows them to identify bottlenecks, construct heatmaps and manage performance/KPIs/goals not only within one plant, but also across different plants and at the enterprise level. Consider how much quicker the Operations Director can zero in on the issues that matter most and best increase efficiency and performance within the shortest possible time.
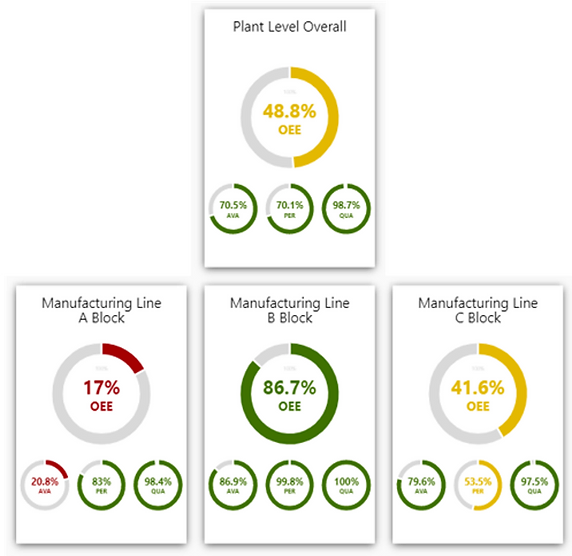
Open sharing of good practices within and across plants
With the flexibility to have a bird’s-eye view of the organisation’s aggregate performance or narrow the aperture to each plant, Operations Directors and Factory Managers can easily identify good practices/ high performing lines and individuals, and facilitate information sharing/ cross-training between them and others so that the performance of the entire entity can be uplifted.
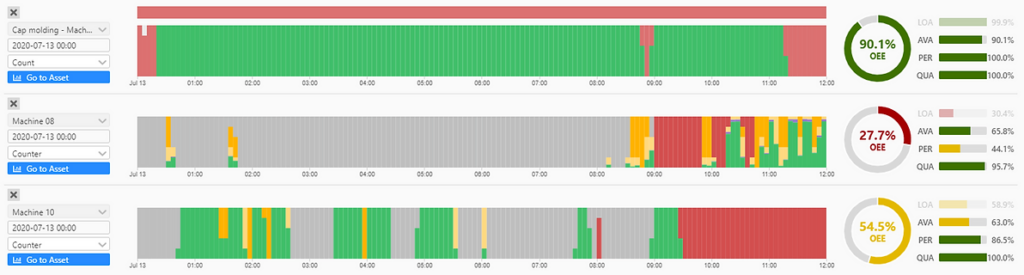
Greater transparency, more learning and less finger-pointing
By relying on real-time data from each equipment as the single source of truth, factory managers and operations directors are sure that the data collected is reliable and not biased or possibly manipulated by the data collectors or supervisors when aggregating the data. There would also be less finger-pointing when engaging in performance improvement dialogues across different departments—that is, for example, the maintenance team and production team pushing the blame to each other regarding some equipment breakdown—because the data provides clear evidence on the parties who are responsible. With less time spent on arguments and more on brainstorming, the company cultivates an interactive process of continuous feedback that leads to more radical performance improvements.
Making the correct CapEx and OpEx decisions
Finally, for Operations Directors and Factory Managers planning to make Capital Expenditures (CapEx) and Operating Expenditures (OpEx) decisions, accurate and reliable real-time data also come in handy. Real-time data provides factual information on the performance of current physical assets and whether new investments are needed. If yes, what kind of investments to make and the percentage of future growth that can be expected from them.
Benefits of I4.0 technologies: for Engineering/Maintenance Manager
Minimising equipment downtime with cost-effective maintenance strategies
Condition-based maintenance (CbM) refers to maintenance taken based on the actual conditions of an asset. Unnecessary maintenance tasks and costs can be avoided with CbM because it strictly dictates that maintenance should only be performed when there is evidence of assets showing abnormal behaviours, decreasing performance or signs of upcoming failures. For the same reason, CbM usually results in longer asset life expectancy than reactive or time-based maintenance strategies.
How exactly does CbM work, you may ask. First, Industrial IoT technologies collect data in real-time from machines and sensors—this is akin to a ‘24/7 health checkup’ for the assets. When anomalies that usually precede equipment failures occur or critical process parameters (e.g. pressure, temperature or vibrations) are breached, alerts would be automatically sent to the Engineers and Maintenance Managers. They are then able to intervene and respond immediately to prevent unexpected breakdowns from happening.
Other than CbM, there is also Predictive maintenance (PdM) which forecasts machine and asset failures using information and data to predict potential equipment failures ahead of time. However, since current Machine Learning (ML) models and algorithms have yet to mature, PdM is still in the introduction stage and not widely adopted.
Benefits of I4.0 technologies: for Process Engineers and Schedulers
Load levelling to reduce setup and changeover times
Customer demands are changing faster than ever before—new products and product variants are constantly developed and needed for different markets. This calls for a wider variety of products to be produced, and hence more frequent changeovers. Yet, manufacturers are expected to maintain a short lead time with the same set of resources; those unable to stay competitive are often ‘dropped’ by customers. Historically, such ‘high mix, mid-high volume’ orders were one major pain point for many manufacturers due to the high setup and changeover times involved.
Through the vertical and horizontal implementation of Industry 4.0 technologies, however, Process Engineers and Schedulers are ‘connected’ to the entire value-chain—they receive clear information on all the volume orders from clients. This interoperability of data enables Process Engineers and Schedulers to decide how best to load level by products so the time taken to changeover a process from running one family of products to running another would be greatly reduced.
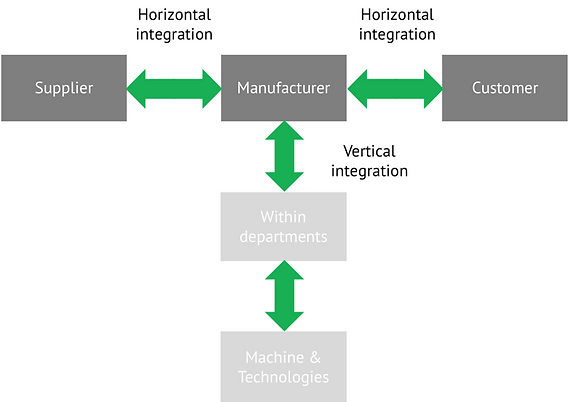
Reacting rapidly to problems on the production lines
To the naked eyes, repetitive mistakes that are causing stoppages and wastage cannot be easily spotted. With real-time data displayed on a dashboard, however, the Process Engineers and Schedulers are not only able to easily spot a bottleneck on the production lines but also be alerted to the areas of Availability, Performance and Quality that are most impacting Overall Equipment Effectiveness (OEE). Such real-time feedback from the production floor allows the process engineers to easily benchmark current output against the planned output to determine if catch ups are required. If so, they can work with the Schedulers and Line Managers to agree on the appropriate resources to be deployed.
Keeping tabs on Critical Control Points and Other Parameters
Additionally, Industry 4.0 technologies enable critical control points (CCP) and parameters data points to be collected round the clock and plotted on control charts to ensure process capability and stability. For example, the viscosity of a batch of jam is constantly monitored so any time the value is out of control, the process engineers will be alerted to examine what went wrong and stop the operators from feeding them into the filler. Should these data be required for compliance or other purposes, they can be easily retrieved from the in-house data centre or on-cloud.
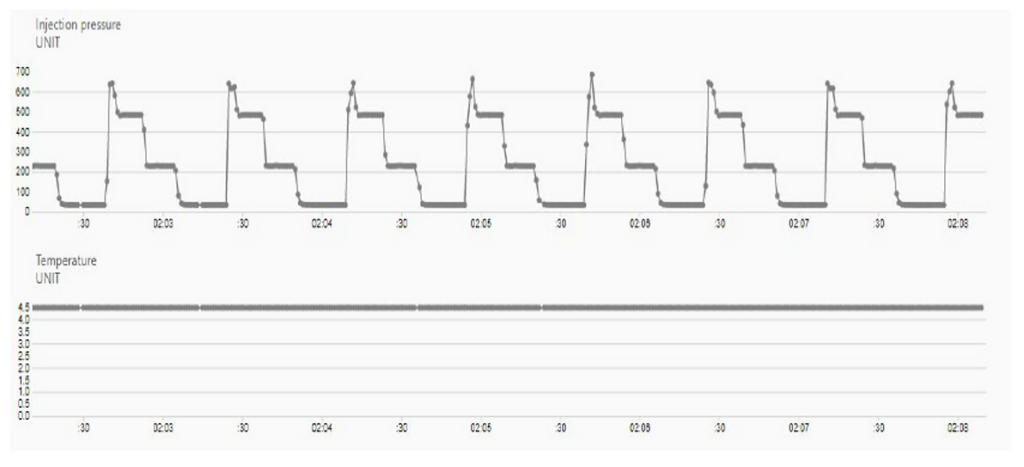
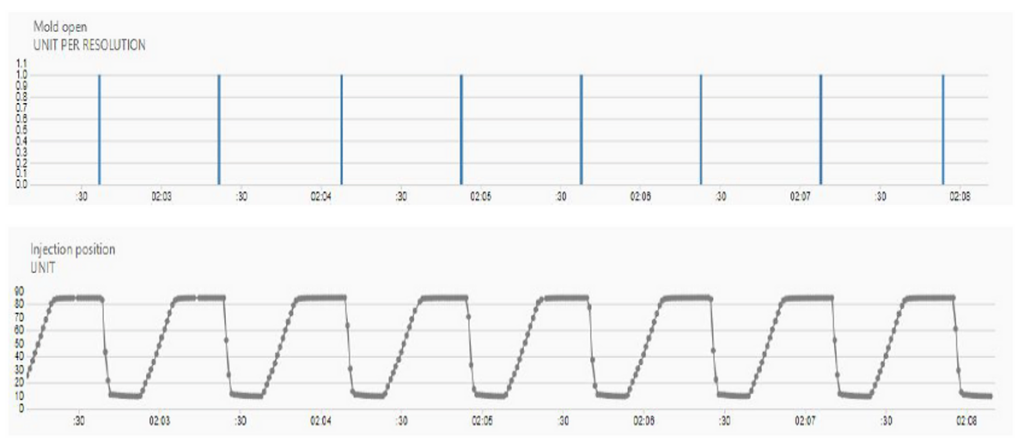
Benefits of I4.0 technologies: for Operators
Empowered to do better
There is only so much automation and technologies can do without humans. Operators are the key resource of any manufacturer—they are experts of their jobs and play a crucial role in the factory’s efficiency, productivity and digital transformation success. There are huge opportunities present when Industry 4.0 technologies are rolled out in parallel with the growth and development of operators.
“The reason for Industry 4.0’s stellar results lies not in its cutting-edge technologies but its emphasis on strong technology-human collaboration.”
Firstly, the flow of working can be greatly improved through automation of rote tasks so operators have more time to focus on what is more important such as making informed decisions through easily accessible data and analytics such as visualisation and simulation tools. Secondly, operators’ performances are monitored and measured in real-time so they can receive honest feedback. Many Operators do initially grapple with the thought and pressure of being monitored—“Why must I be under surveillance? Is the boss unhappy with my performance?” However, after understanding that the purpose of doing so is to provide them with opportunities to independently monitor and assess the progress they have made towards their goals, the majority of them are excited for it. Finally, feedback does not only have to be negative—positive feedback based on unbiased data should be given just as frequently to recognise operators for their good performance and encourage them to double down on what is good.
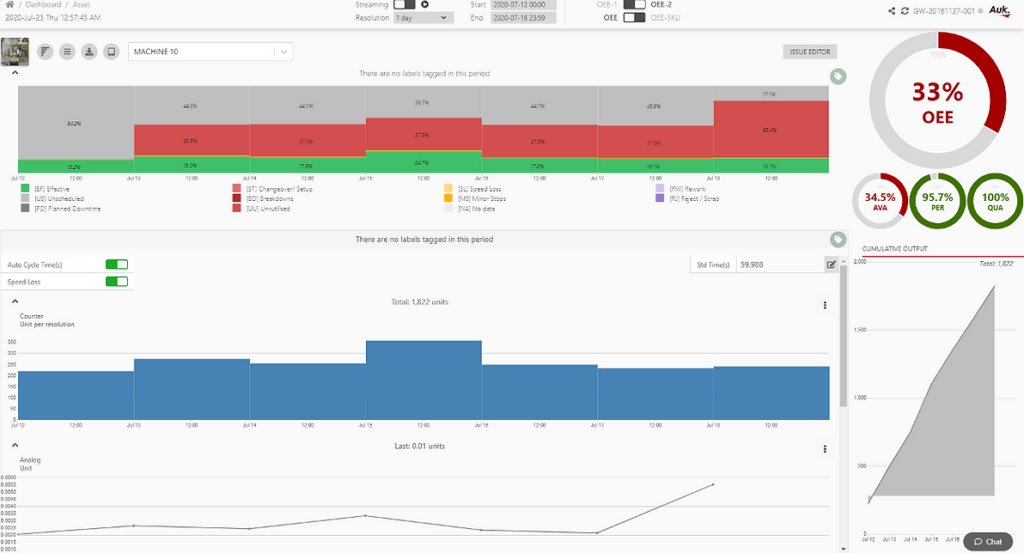
“Monthly feedback is too infrequent. Weekly feedback is not good enough. If we have difficulties recalling what happened a few days ago, we cannot expect operators to remember what affected their production performance months or even weeks ago. Manufacturers should give operators real-time feedback to their performance after every shift and day while the day is still fresh in their minds.”
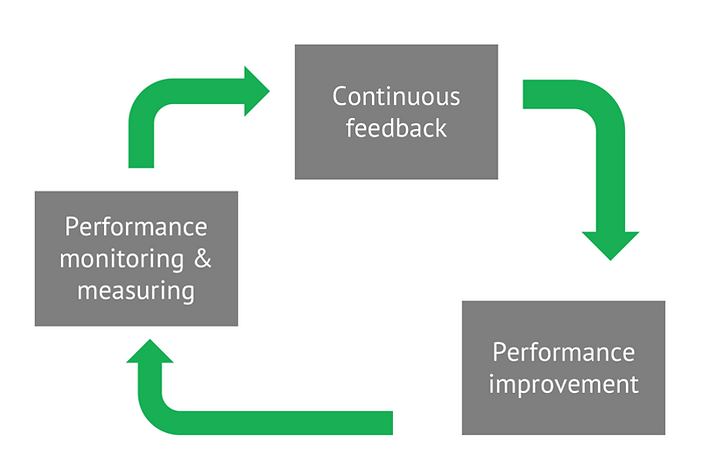
Engaged to drive higher performance in the factory
Industry 4.0 technologies provide a plethora of data, data synthesising, and analysis but it does not stop here. Through interconnectedness, there is democratisation of data where information can flow to the operators and knowledge is generated when they are applied and used for strategic decision making and problem-solving.
When Key Performance Indicators (KPIs) and metrics such as daily production level and Overall Equipment Effectiveness (OEE) are calculated and made visible synchronously, they not only serve as an impetus to motivate operators to work better but also engage operators more in the macro-production performance of the factory. With greater visibility on the performance of different production lines, there are more opportunities for Operators to spot anomalies on the production floor and report them to their Line Managers.
Overcoming the challenges of Industry 4.0
Against the backdrop of ongoing productivity optimisation and a greater focus on customer-specific adaptation, Industry 4.0 presents several opportunities and advantages for manufacturers. Nonetheless, some challenges would also emerge when transitioning to Industry 4.0 which manufacturers should take note and respond accordingly.
High initial investment
Manufacturers should expect that Industry 4.0 solutions do require considerable investment. However, with mass production, the prototypical cost curve should flatten out and the initial investments can be recouped over time. Those who decide to forge ahead could consider setting aside some planned new capital investments and kickstart the digital transformation process by pilot testing or starting small (e.g. begin with a few production lines) first.

Skilled workers demanded
Highly skilled and digitally-skilled workers are necessary to manage and control the integrated operations brought about by Industry 4.0. As such, manufacturers must support, train and upskill their operators with a new set of skills to adapt to the usage and effects of technologies lest they become alienated.
Conclusion
By adopting Industry 4.0 into the increasingly complex manufacturing scene, manufacturers can expect fewer inefficiencies and waste both upstream and downstream. Real-time monitoring of operations provides round-the-clock visibility into different performance metrics and potential problems so actions can be taken to resolve them. Industry 4.0 brings about positive impact beyond the four walls of the factory – when manufacturers are better equipped to meet the unique needs of their customers, customer loyalty and satisfaction also increases. Success does not come easy but those who navigate through the initial hiccups and challenges would see light at the end of the tunnel.